Adhesive / sealant/ Bonding flame retardants application
Construction field: Installation of fire doors, firewalls, fire boards
Electronic and electrical field: Circuit boards, electronic components
Automotive industry: Seats, dashboards, door panels
Aerospace field: Aviation instruments, spacecraft structures
Household items: Furniture, floors, wallpapers
Flame Retardant Adhesive Transfer Tape: Excellent for metals, foams and plastics such as polyethylene
Functioning of Flame Retardants
Flame retardants inhibit or delay the spread of fire by suppressing the chemical reactions in the flame or by the formation of a protective layer on the surface of a material.
They may be mixed with the base material (additive flame retardants) or chemically bonded to it (reactive flame retardants). Mineral flame retardants are typically additive while organic compounds can be either reactive or additive.
Designing Fire-Retardant Adhesive
A fire effectively has four stages:
Initiation
Growth
Steady State, and
Decay
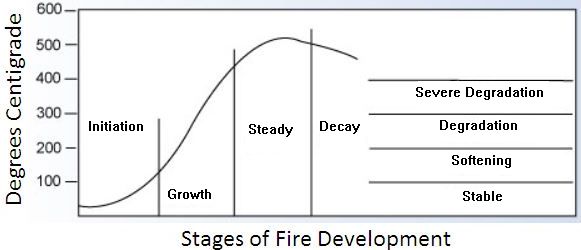
Comparison of the Degradation Temperatures of a Typical Thermoset Adhesive
With Those Reached in Various Stages of a Fire
Each state has a corresponding degradation temperature as shown in Figure. In designing a fire-retardant adhesive, formulators must put their efforts on delivering temperature resistance on the right fire stage for the application:
● In electronic manufacturing, for example, an adhesive must suppress any tendency of the electronic component to catch fire - or initiate - if there is a fault-induced rise in temperature.
● For bonding tiles or panels, adhesives need to resist detachment in the growth and steady state stages, even when in direct contact with the flame.
● They must also minimize toxic gases and smoke emitted. Load-bearing structures are likely to experience all four stages of the fire.
Limiting Combustion Cycle
To limit the combustion cycle, one or several of the processes contributing to fire must be removed by either:
● Elimination of the volatile fuel, as by cooling
● Production of a thermal barrier, as by charring, thus eliminating fuel by reducing heat transfer, or
● Quenching the chain reactions in the flame, as by adding suitable radical scavengers
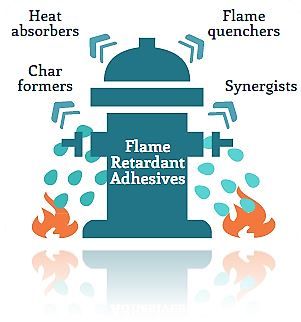
Flame retardant additives do this by acting chemically and/or physically in the condensed (solid) phase or in the gas phase by providing one of the following functions:
● Char formers: Usually phosphorus compounds, which remove the carbon fuel source and provide an insulation layer against the fire’s heat. There are two char forming mechanisms:
Redirection of the chemical reactions involved in decomposition in favor of reactions yielding carbon rather than CO or CO2 and
Formation of a surface layer of protective char
● Heat absorbers: Usually metal hydrates, such as aluminum trihydrate or magnesium hydroxide, which remove heat by the evaporation of water from the flame retardant’s structure.
● Flame quenchers: Usually bromine- or chlorine-based halogen systems which interfere with the reactions in a flame.
● Synergists: Usually antimony compounds, which enhance performance of the flame quencher.
Significance of Flame Retardants in Fire Protection
Flame retardants are an important part of fire protection as they not only reduce the risk of a fire starting, but also that of its propagation. This increases escape time and, thus, protects humans, property, and the environment.
There are many ways to establish an adhesive as a fire retardant. Let's understand the classification of flame retardants in detail.
The requirement for fire retardant adhesives is increasing and their use expands to a number of different industry sectors examples including aerospace, construction, electronics and public transport (trains in particular).
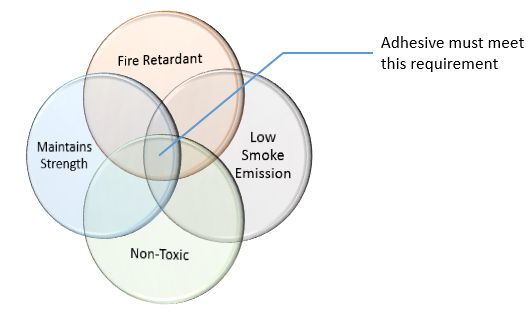
1: So, one of the obvious key criteria is to be flame resistant / non-burning or, better still, inhibit flames – properly fire retardant.
2: The adhesive should not give off excessive or toxic smoke.
3: The adhesive needs to maintain its structural integrity at high temperatures (have as good a temperature resistance as possible).
4: Decomposed adhesive material should not contain toxic by-products.
It looks like a tall order to come up with an adhesive that can match these requirements – and at this stage, viscosity, colour, cure speed and preferred cured method, gap fill, strength performance, thermal conductivity, and packaging haven’t even been considered. But the development chemists enjoy a good challenge so BRING IT ON!
Environment regulations tend to be industry and region-specific
A large group of the studied flame retardants has been found to have a good environmental and health profile. These are:
● Ammonium polyphosphate
● Aluminum diethylphosphinate
● Aluminum hydroxide
● Magnesium hydroxide
● Melamine polyphosphate
● Dihydrooxaphosphaphenanthrene
● Zinc stannate
● Zinc hydroxstannate
Flame retardancy
Adhesives can be developed to match a sliding scale of fire retardancy – here are details of the Underwriters Laboratory Testing classifications. As adhesive manufacturers, we are seeing requests mainly for the UL94 V-0 and occasionally for the HB.
UL94
● HB: slow burning on a horizontal specimen. Burn rate <76mm/min for thickness <3mm or burning stops before 100mm
● V-2: (vertical) burning stops in <30 seconds and any drips may be flaming
● V-1: (vertical) burning stops in <30 seconds, and drips are allowed (but must not be burning)
● V-0 (vertical) burning stops in <10 seconds, and drips are allowed (but must not be burning)
● 5VB (vertical plaque specimen) burning stops in <60 seconds, no drips; specimen may develop a hole.
● 5VA as above but not allowed to develop a hole.
The two latter classifications would pertain to a bonded panel rather than a specimen of adhesive.
The testing is pretty simple and doesn’t require sophisticated equipment, here is a basic test setup:
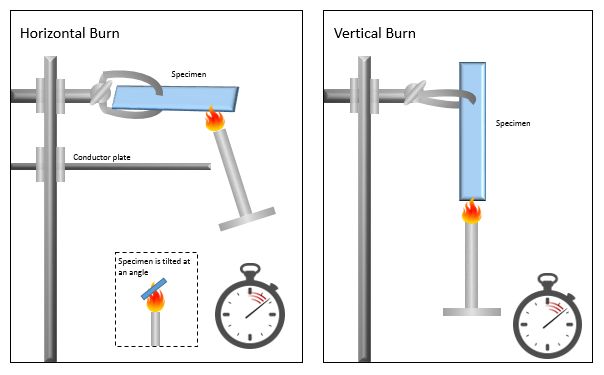
It can be quite tricky to do this test on some adhesives alone. Particularly for adhesives that won’t cure properly outside of a closed joint. In this case, you can test only between bonded substrates. However, epoxy glue and UV adhesives can be cured as a solid test specimen. Then, insert the test specimen into the jaws of the clamp stand. Keep a sand bucket nearby, and we strongly recommend doing this under extraction or in a fume cupboard. Don’t set off any smoke alarms! Especially those linked directly to the emergency services. Catch the specimen on fire and time how long it takes for the flame to extinguish. Check for any drips underneath (hopefully, you have a disposable tray in situ; otherwise, bye-bye nice worktop).
Adhesive chemists combine a number of additives to make fire retardant adhesives – and sometimes even to quench flames (although this feature is harder to achieve nowadays with many goods manufacturers now requesting halogen-free formulations).
Additives for fire resistant adhesives include
● Organic char-forming compounds which help to lower heat and smoke and protect the material underneath from further burning.
● Heat absorbers, these are normal metal hydrates which help give the adhesive great thermal properties (often, the fire retardant adhesives are selected for heat sink bonding applications where maximum thermal conductivity is required).
It is a careful balance as these additives will cause interference with other adhesive properties such as strength, rheology, cure speed, flexibility etc.
Is there a difference between fire resistant adhesives and fire retardant adhesives?
Yes! There is. Both terms have been bandied about in the article, but it is probably best to set the story straight.
Fire resistant adhesives
these are often products such as inorganic adhesive cements and sealants. They don’t burn and they withstand extreme temperatures. Applications for these types of products include, blast furnaces, ovens etc. They don’t do anything to stop an assembly burning. But they do a great job of holding all the burning bits together.
Fire retardant adhesives
These help to extinguish the flames and slow the spread of fire.
Many industries seek these types of adhesives
● Electronics – for potting and encapsulating electronics, bonding heat sinks, circuit boards etc. An electronic short circuit can easily spark a fire. But PCBs contain fire retardant compounds – it is often important that adhesives also have these properties.
● Construction – cladding and flooring (particularly in public areas) often has to be non-burning and bonded with a fire retardant adhesive.
● Public transport – train carriages, bus interiors, trams etc. Applications for Flame retardant adhesives include bonding composite panels, flooring, and other fixtures and fittings. Not only do the adhesives help stop the spread of fire. But they provide an aesthetic joint without the need for unsightly (and rattly) mechanical fasteners.
● Aircraft – as mentioned earlier, cabin interior materials are under strict regulations. They must be fire retardant and not fill the cabin with black smoke during a fire.
Standards and Test Methods for Flame Retardants
Standards related to fire testing are aimed at determining the performance of a material with respect to flame, smoke, and toxicity (FST). Several tests have been widely used to determine the resistance of materials to these conditions.
Selected Tests for Flame Retardants
Resistance to Burning |
|
ASTM D635 | “Rate of Burning of Plastics” |
ASTM E162 | “Flammability of Plastic Materials” |
UL 94 | “Flammability of Plastic Materials” |
ISO 5657 | “Ignitability of Building Products” |
BS 6853 | “Flame Propagation” |
FAR 25.853 | “Airworthiness Standard – Compartment Interiors” |
NF T 51-071 | “Oxygen Index” |
NF C 20-455 | “Glow Wire Test” |
DIN 53438 | “Flame Propagation” |
Resistance to High Temperatures |
|
BS 476 Part No. 7 | “Surface Spread of Flame – Building Materials” |
DIN 4172 | “Fire Behaviors of Building Materials” |
ASTM E648 | “Floor Coverings – Radiant Panel” |
Toxicity |
|
SMP 800C | “Toxicity Testing” |
BS 6853 | “Smoke Emission” |
NF X 70-100 | “Toxicity Testing” |
ATS 1000.01 | “Smoke Density” |
Smoke Generation |
|
BS 6401 | “Specific Optical Density of Smoke” |
BS 6853 | “Smoke Emission” |
NES 711 | “Smoke Index of Products of Combustion” |
ASTM D2843 | “Smoke Density from Burning Plastics” |
ISO CD5659 | “Specific Optical Density – Smoke Generation” |
ATS 1000.01 | “Smoke Density” |
DIN 54837 | “Smoke Generation” |
Testing Resistance to Burning
In most tests that measure the resistance to burning, suitable adhesives are those that do not continue to burn for any significant period after removal of the source of ignition. In these tests the cured adhesive sample may be subjected to ignition independent of any adherend (the adhesive is tested as a free film).
Although this approach does not simulate practical reality, it does provide useful data on the relative resistance of the adhesive to burning.
Sample structures with both adhesive and adherend can also be tested. These results may be more representative of the performance of the adhesive in an actual fire since the contribution provided by the adherend could be either positive or negative.
UL-94 Vertical Burning Test
It provides a preliminary assessment of relative flammability and dripping for polymers used in electrical equipment, electronic devices, appliances, and other applications. It addresses such end-use characteristics of ignition, burn rate, flame spread, fuel contribution, intensity of burning, and products of combustion.
Working and Set Up - In this test a film or coated substrate sample is mounted vertically in a draft free enclosure. A burner is placed beneath the sample for 10 seconds and the duration of flaming is timed. Any dripping that ignites surgical cotton placed 12 inches below the sample is noted.
The test has several classifications:
94 V-0: No specimen has flaming combustion for more than 10 seconds after ignition. Specimens do not burn up to the holding clamp, drip and ignite the cotton, or have glowing combustion persisting for 30 seconds after removal of the test flame.
94 V-1: No specimen shall have flaming combustion for over 30 seconds after each ignition. Specimens do not burn up to the holding clamp, drip and ignite the cotton, or have an afterglow of more than 60 seconds.
94 V-2: This involves the same criteria as V-1, except that the specimens are allowed to drip and ignite the cotton below the specimen.
Other Strategies for Measuring Burning Resistance
Another method for measuring the burning resistance of a material is to measure the limiting oxygen index (LOI). The LOI is the minimum concentration of oxygen expressed as a volume percent of mixture of oxygen and nitrogen that just supports flaming combustion of a material initially at room temperature.
The resistance of an adhesive to high temperatures in the case of a fire needs special consideration aside from the flame, smoke, and toxicity effects. Often the substrate will protect the adhesive from a fire. However, if the adhesive loosens or degrades due to the temperature of the fire, the joint can fail causing separation of the substrate and the adhesive. If this happens, the adhesive itself becomes exposed together with the secondary substrate. These fresh surfaces then can contribute further to the fire.
The NIST smoke density chamber (ASTM D2843, BS 6401) is used widely in all industrial sectors for the determination of smoke generated by solid materials and assemblies mounted in the vertical position within a closed chamber. Smoke density is measured optically.
When an adhesive is sandwiched between two substrates, the fire resistance and thermal conductivity of the substrates control the decomposition and smoke emission of the adhesive
In smoke density tests, adhesives can be tested alone as a free coating to impose a worst case condition.
Find Suitable Flame Retardant Grade
View a wide range of flame retardant grades available in the market today, analyze technical data of each product, get technical assistance or request samples.
TF-101, TF-201, TF-AMP